来源于:中国冶金报
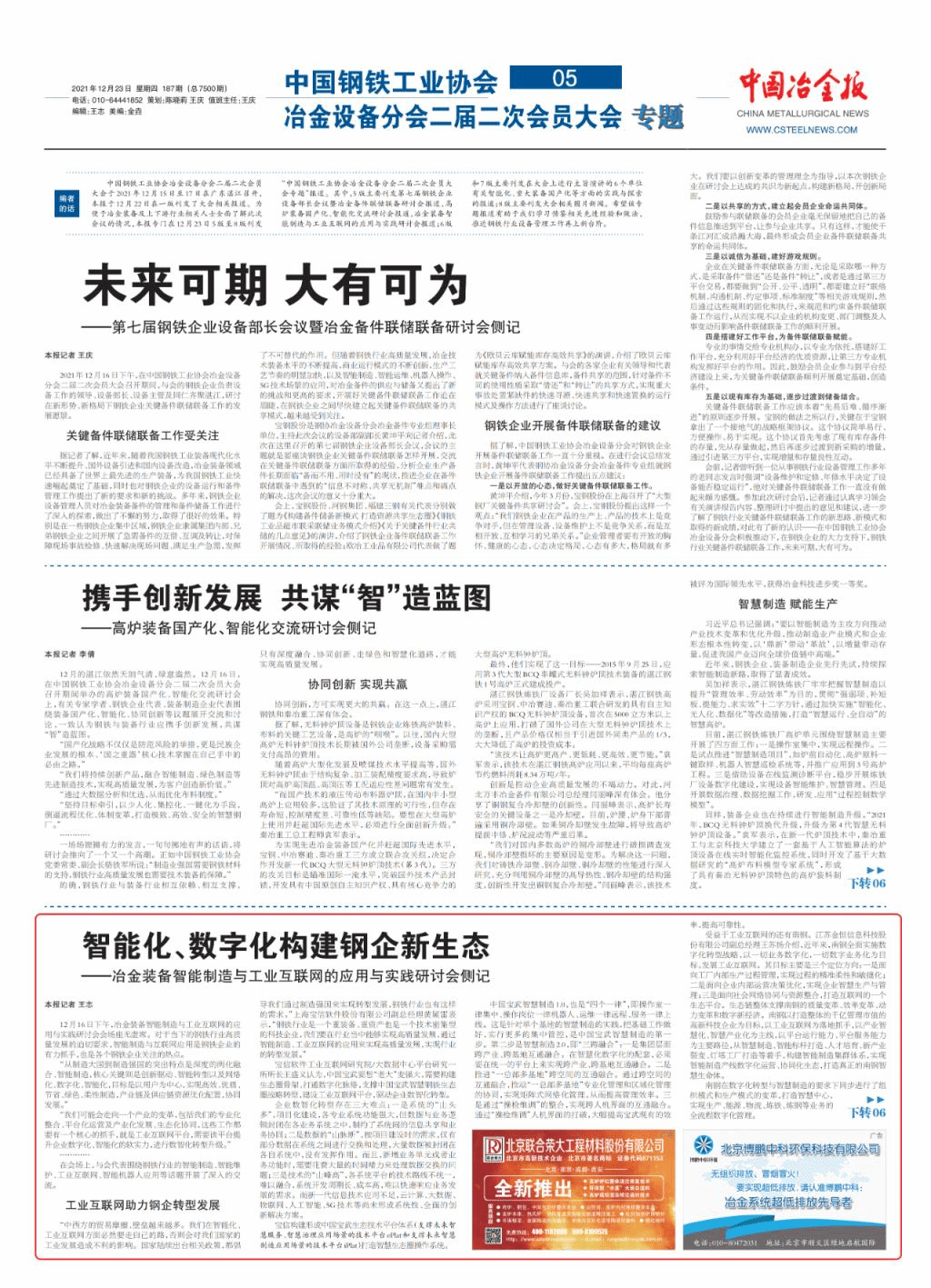
12月16日下午,冶金装备智能制造与工业互联网的应用与实践研讨会会场座无虚席。对于当下的钢铁行业高质量发展的迫切要求,智能制造与互联网应用是钢铁企业的有力抓手,也是各个钢铁企业关注的热点。
“从制造大国到制造强国的突出特点是深度的两化融合、智能制造,核心关键则是创新驱动、智能转型以及网络化、数字化、智能化,目标是以用户为中心,实现高效、优质、节省、绿色、柔性制造,产业链及供应链资源优化配置,协同发展。”
“我们可能会走向一个产业的变革,包括我们的专业化整合、平台化运营及产业化发展、生态化协同,这些工作都要有一个核心的抓手,就是工业互联网平台,需要该平台提升企业数字化、智能化的软实力,进行数智化转型升级。”
…………
在会场上,与会代表围绕钢铁行业的智能制造、智能维护、工业互联网、智能机器人应用等话题开展了深入的交流。
工业互联网助力钢企转型发展
“中西方的贸易摩擦、壁垒越来越多。我们在智能化、工业互联网方面必然要走自己的路,否则会对我们国家的工业发展造成不利的影响。国家陆续出台相关政策,都倡导我们通过制造强国来实现转型发展,钢铁行业也有这样的需求。”上海宝信软件股份有限公司副总经理黄颖雷表示,“钢铁行业是一个重装备、重资产也是一个技术密集型的科技企业,我们要在行业当中能够实现高质量发展,通过智能制造、工业互联网的应用来实现高质量发展,实现行业的转型发展。”
宝信软件工业互联网研究院/大数据中心平台研究一所所长王盛义认为,中国宝武要想“老大”变强大,需要构建生态圈骨架、打通数字化脉络,支撑中国宝武智慧钢铁生态圈战略转型,建设工业互联网平台,驱动企业数智化转型。
企业数智化转型存在三大难点:一是系统的“山头多”,项目化建设,各专业系统功能强大,但数据与业务逻辑封闭在各业务系统之中,制约了系统间的信息共享和业务协同;二是数据的“山脉断”,按项目建设时的需求,仅有部分数据在系统之间进行交换和处理,大量数据被封闭在各自系统中,没有发挥作用。而且,新增业务单元或者业务功能时,需要花费大量的时间精力来处理数据交换的问题;三是技术的“山峰高”,各系统平台的技术路线不统一,难以融合,系统开发周期长、成本高,难以快速响应业务发展的需求。而新一代信息技术应用不足,云计算、大数据、物联网、人工智能、5G技术等尚未形成系统性、全面的创新解决方案。
宝信构建形成中国宝武生态技术平台体系(支撑未来智慧服务、智慧治理应用场景的技术平台ePlat和支撑未来智慧制造应用场景的技术平台iPlat)打造智慧生态圈操作系统。
中国宝武智慧制造1.0,也是“四个一律”,即操作室一律集中、操作岗位一律机器人、运维一律远程、服务一律上线。这是针对单个基地的智慧制造的实践,把基础工作做好,实行更多的集中管控,是中国宝武智慧制造的第一步。第二步是智慧制造2.0,即“三跨融合”:一是集团层面跨产业、跨基地互通融合。在智慧化数字化的配套,必须要在统一的平台上来实现跨产业、跨基地互通融合。二是推进“一总部多基地”跨空间的互通融合。通过跨空间的互通融合,推动“一总部多基地”专业化管理和区域化管理的协同,实现矩阵式网络化管理,从而提高管理效率。三是通过“操检维调”的整合,实现跨人机界面的互通融合。通过“操检维调”人机界面的打破,大幅提高宝武现有的效率,提高可靠性。
受益于工业互联网的还有南钢。江苏金恒信息科技股份有限公司副总经理王苏扬介绍,近年来,南钢全面实施数字化转型战略,以一切业务数字化,一切数字业务化为目标,发展工业互联网。其目标主要是三个定位方向:一是面向工厂内部生产过程管理,实现过程的精准柔性和敏捷化;二是面向企业内部运营决策优化,实现企业智慧生产与管理;三是面向社会网络协同与资源整合,打造互联网的一个生态平台。生态链整体支撑南钢的质量变革、效率变革、动力变革和数字新经济。南钢以打造整体的千亿管理市值的高新科技企业为目标,以工业互联网为落地抓手,以产业智慧化、智慧产业化为主线,以平台运行能力、平台服务能力为主要路径,从智慧制造、智能标杆打造、人才培育、新产业裂变、灯塔工厂打造等着手,构建智能制造集群体系,实现智能制造产线数字化运营、协同化生态,打造真正的南钢智慧生命体。
南钢在数字化转型与智慧制造的要求下同步进行了组织模式和生产模式的变革,打造智慧中心,实现生产、能源、物流、炼铁、炼钢等业务的全流程数字化管理。
工业互联网的发展推进了集中控制的发展。宝信软件工业互联网研究院高级总监徐永军介绍,集中控制实现产线、工序极致效率,专业集中管理,支撑管理变革与流程再造;实现制造、设备、能环、物流、安保协同管控体系,支撑公司、厂部调度扁平化管控;集中控制推动多基地同工序技术能力共同提升;支撑与赋能专业化整合。
其中,操业集控是以流程再造及组织变革为顶层设计,基于大数据、物联网、人工智能等新技术,实现大规模、远距离的集中监视、操控以及功能与软件重构、数据创新应用;操业集控分为产线、工序、公辅3种集控类型。
管理集控构建基地“统一、高效、集中、专业”的平台,集“调度、管控、指挥、发布”于一体,有机集成制造、设备、能环、物流、安保业务,形成五合一协同管控体系,贯穿原料进厂、生产制造、成品出厂的业务管理;高效整合公司、厂部二级调度,精简岗位,实现扁平化管控。
多基地专业管控是指搭建跨基地专业运行平台,实现不同基地相同工序内数据互联、智能远程诊断、关键KPI对标、知识互联互通,推动多基地同工序技术能力共同提升,赋能工序管理和技术创新变革。
“集中控制的顶层设计一定是流程优化和岗位重塑,这是我们的一个初心,无人化、少人化、一键化和产线的高度自动化是集中控制的基础。”徐永军说道。
集中控制未来会怎么走?徐永军认为,移动操作会成为一种主流,传统操作室会逐步地弱化,不会取消,大屏的数量和固定终端数量会减少,未来的集中控制面向对象、面向过程,管理界面和操作界面形成统一,一个屏、一个手机就够了。
在操作智能上,实现机理模型与专家支撑的操业导航,AI基于大数据提出操作决策,如配料等。最后要做到无人化工厂即黑屏工厂,操作工由原来“高度介入型”变成“值守型”,只在异常处理和异常阶段紧急处理时候需要介入。
冶金智能装备是冶金工业智能化的一部分。随着智能化的发展,钢铁企业根据实际的生产应用,纷纷研究出了机器人,将人从危险和劳动量大的工作岗位替换出来,发挥着重要作用。莱钢电子自动化事业部副经理李振刚在会上介绍了莱钢应用的几款机器人及系统,例如自主研发的废钢无人天车系统综合利用激光扫描成像、测距、防摇、防撞、工业无线通讯、地面安全等技术,实现行车的无人化,自动作业,实现库区无人操作、自动运行,减少行车操作和地面库区管理人员数量、提升劳动效率、保障人身安全,为企业降本增效。
转炉防溢渣视觉分析预警系统在出钢过程中实时判断炉口下渣情况,根据图像特征分为正常、溢渣预警和溢渣。当检测到炉内钢渣大炉口溢渣风险时,触发系统预警,控制自动出钢系统会及时停止倾炉,帮助作业人员全面掌握炉口下渣情况,实现了转炉出钢过程的实时监控、智能判断、动态控制。
鱼雷罐车插头视觉识别自动拔插机器人系统,实现了罐车插头的二维视觉识别以及3D视觉精确定位功能,配合罐号标识自动识别及大数据管理系统,能够实现所有鱼雷罐车插头的全自动定位、拔插功能。
王苏扬介绍,智能装备也是南钢数字化转型中的重要应用,是支撑南钢工业互联网的数据和应用的基础之一,在智能装备应用方面,南钢已经有覆盖全产线的冶金工业机器人,从炼铁、炼钢到轧钢经典工位都有相应的智能制造产品。例如炼铁无人抓渣行车、炼钢测温取样机器人、焊标牌机器人、连铸加保护渣机器人以及智能实验室机器人等,其中自主研发设计的实验室机器人是对实验室的一个智能化变革,也是智慧制造和智能生产的生动实践。